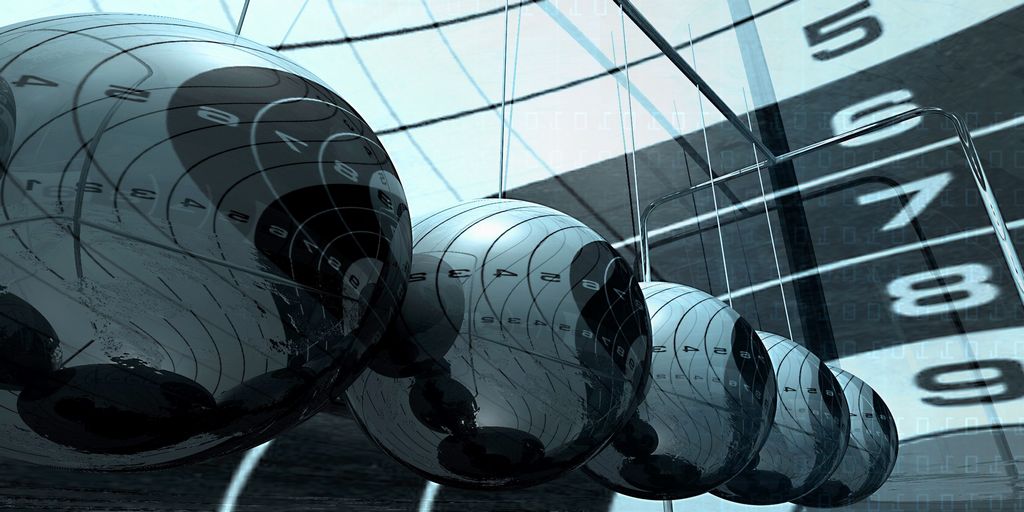
Picture by Piro4D
A Lean Management System (LMS) is a method of managing an organization that focuses on reducing waste, streamlining processes, and increasing efficiency. It is based on the idea that by eliminating non-value adding activities, an organization can become more productive and profitable. The goal of a Lean Management System is to identify and reduce waste, improve efficiency and productivity, and increase customer satisfaction.
The Lean approach was first developed by Toyota in the late 1940s as part of its production system. Since then, it has become a widely adopted management system in manufacturing, healthcare, government, and service organizations. It has been used to improve customer service, reduce cost, and increase product quality. The core principles of Lean are:
The Lean approach was first developed by Toyota in the late 1940s as part of its production system. Since then, it has become a widely adopted management system in manufacturing, healthcare, government, and service organizations. It has been used to improve customer service, reduce cost, and increase product quality. The core principles of Lean are:
1. Identify and Eliminate Waste
Waste is defined as anything that does not add value to the customer. Lean focuses on eliminating activities that don’t add value, such as overproduction, waiting, defects, and excess inventory.
2. Continuous Improvement
Lean is based on the idea of continuous improvement. This means that an organization should always be looking for ways to make their processes more efficient and effective.
3. Focus on the Customer
The customer should always be at the center of any organization’s strategy and decision-making. Lean emphasizes the need to understand and meet customer needs.
4. Respect for People
People are a key part of any organization and should be respected and empowered. Lean encourages teams to work together to identify and solve problems, and promote a culture of respect and open communication.
5. Process-Oriented
Lean emphasizes the importance of understanding and improving processes. This involves analyzing processes to identify where there is waste and inefficiency, and then implementing improvements.
Implementing a Lean Management System can help an organization increase its efficiency, reduce costs, and improve customer satisfaction. It can also help an organization become more agile and responsive to changes in the market. Additionally, Lean can help to create an environment where employees are more engaged, motivated, and productive. The benefits of implementing a Lean Management System include:
Implementing a Lean Management System can help an organization increase its efficiency, reduce costs, and improve customer satisfaction. It can also help an organization become more agile and responsive to changes in the market. Additionally, Lean can help to create an environment where employees are more engaged, motivated, and productive. The benefits of implementing a Lean Management System include:
• Increase Efficiency
Lean helps to identify and eliminate non-value-adding activities, resulting in improved efficiency and productivity.
• Reduce Costs
Eliminating waste and streamlining processes can help to reduce costs.
• Improve Quality
Lean focuses on identifying and eliminating defects, resulting in higher quality products and services.
• Increase Customer Satisfaction
By focusing on customer needs and eliminating waste, organizations can improve customer satisfaction.
• Create a Culture of Continuous Improvement
Lean encourages teams to work together to identify and solve problems and promote a culture of continuous improvement.
A Lean Management System is a method of managing an organization that focuses on reducing waste, streamlining processes, and improving efficiency. It can help organizations become more efficient, reduce costs, and improve customer satisfaction. Implementing a Lean Management System can help organizations become more agile and responsive to changes in the market, and create an environment where employees are more engaged, motivated, and productive. Here are the 7 steps to implement a Lean Management System:

A Lean Management System is a method of managing an organization that focuses on reducing waste, streamlining processes, and improving efficiency. It can help organizations become more efficient, reduce costs, and improve customer satisfaction. Implementing a Lean Management System can help organizations become more agile and responsive to changes in the market, and create an environment where employees are more engaged, motivated, and productive. Here are the 7 steps to implement a Lean Management System:
Step 1: Identifying the Need for a Lean Management System
The first step to implementing a lean management system is to identify the need for it. This involves assessing the current state of the organization and determining what areas could be improved through the use of lean principles. The organization should consider factors such as customer satisfaction, employee engagement, process efficiency, and overall profitability. By doing so, the organization can identify specific areas of improvement and the need for a lean management system.
Step 2: Establishing a Lean Team
The second step to implementing a lean management system is to establish a lean team. This team should consist of experts from different departments and levels of the organization. The team should be responsible for analyzing and assessing the organization's processes and procedures, and identifying areas of improvement. The team should also be responsible for developing a strategy for implementing the lean management system.
Step 3: Defining a Lean Strategy
The third step to implementing a lean management system is to define a lean strategy. This involves setting out the goals and objectives of the system, and detailing how it will be implemented. The strategy should also include metrics for measuring the success of the system and how it will be monitored.
Step 4: Implementing Lean Principles
The fourth step to implementing a lean management system is to implement the lean principles. This involves applying the principles to all areas of the organization and ensuring that they are adhered to. This includes establishing processes and procedures that are efficient and effective. It also involves training employees in lean principles and ensuring that they have the necessary skills to work in a lean environment.
Step 5: Monitoring the Lean System
The fifth step to implementing a lean management system is to monitor its progress. This involves measuring the success of the system and identifying areas where further improvements can be made. The organization should also pay attention to feedback from employees and customers, as this can help identify areas of improvement.
Step 6: Continuous Improvement
The sixth step to implementing a lean management system is to ensure continuous improvement. This involves regularly assessing the system and making adjustments when necessary. It also involves encouraging employees to take responsibility for their own performance and suggest improvements to the system.
Step 7: Evaluating the System
The seventh step to implementing a lean management system is to evaluate its progress. This involves assessing the success of the system and identifying areas where it can be further improved. The organization should also review the system periodically to ensure that it is meeting the goals and objectives set out in the strategy.
Implementing a lean management system can be a difficult and lengthy process, but the benefits of doing so can be significant. By following these seven steps, organizations can ensure that they are taking all the necessary steps to successfully implement a lean management system and reap the rewards of doing so.
Implementing a lean management system can be a difficult and lengthy process, but the benefits of doing so can be significant. By following these seven steps, organizations can ensure that they are taking all the necessary steps to successfully implement a lean management system and reap the rewards of doing so.